Insights on Advanced Manufacturing and Automation
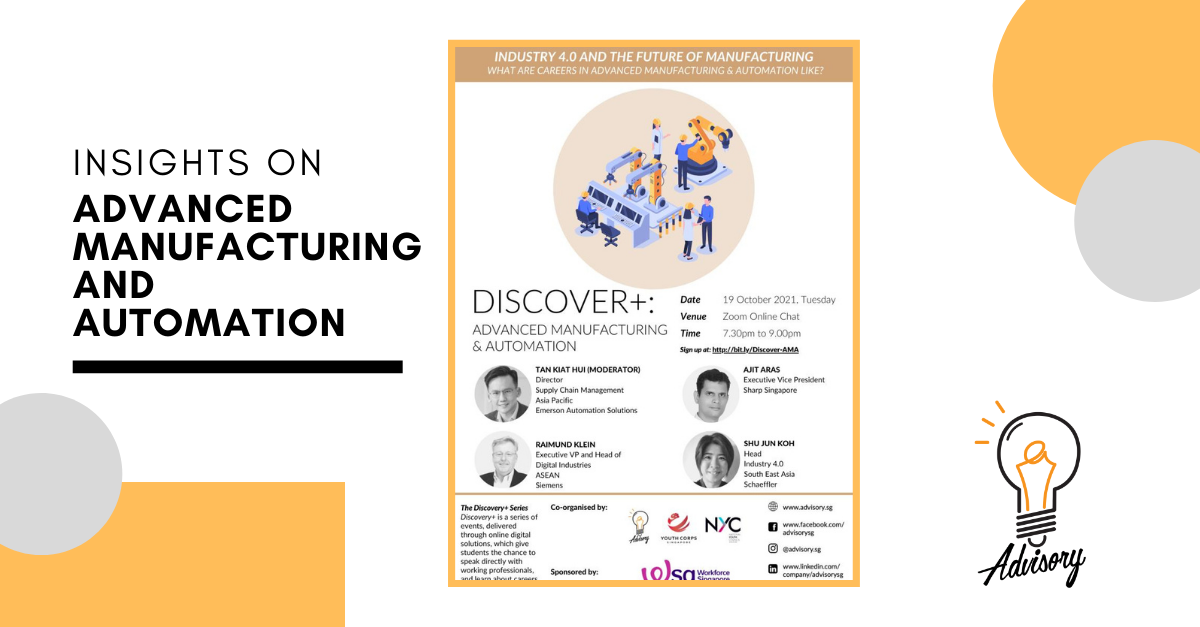
By Adriale Pang
Discovery+ is a series of online industry panels which give students the chance to interact with working professionals and learn about the careers they aspire to enter. These panels provide youths and working professionals with the opportunity to better understand industry trends, hear first-hand perspectives from industry professionals, and gain valuable advice on entering or navigating these industries.
On 19 October 2021, Advisory hosted Discover+: Advanced Manufacturing and Automation, the 44th edition of the Discovery+ series. Speakers on the panel included:
- Tan Kiat Hui (Moderator), Director, Supply Chain Management Asia Pacific, Emerson Automation Solutions
- Ajit Aras, Executive Vice President, Sharp Singapore
- Raimund Klein, Executive VP and Head of Digital Industries, ASEAN, Siemens
- Shu Jun Koh, Head, Industry 4.0, South East Asia, Schaeffler
Attendees included students at various levels of education with a desire to know the different career paths in Advanced Manufacturing and Automation, and how to best position themselves for such roles. Below are some key points shared during the session:
What is advanced manufacturing and automation?
Advanced manufacturing is about manufacturing companies utilising bleeding-edge technology to create solutions for their clients. Many firms face issues such as their factory operations being backward and slow due to the usage of old machinery and processes. These firms may seek the help of manufacturing companies to engineer solutions to address these issues. These solutions may be in the form of products or processes, for example the introduction of 5G-enabled 3D printers into factories. Automation is often a solution that is introduced to boost the productivity of firms, where machines free up human labour for other purposes.
What does a job in advanced manufacturing entail?
A career in advanced manufacturing is primarily about creating solutions for one’s clients. This involves developing products, managing projects, analysing businesses and supply chains, conducting R&D, designing infrastructure, driving operations and automation, enabling mobility, interviewing clients to uncover pain points, crafting a sales pitch for your proposed solution, and much more. It is not just about creating new products, but leveraging existing technology in better ways to help your client move forward.
What are some trends you observe in the manufacturing industry?
The advancement of technology is an obvious trend in manufacturing. It is a very exciting time to be in manufacturing. Some youths may have a misconception that manufacturing is old-school and boring, but the reality is quite the opposite. Advanced technology — such as Artificial Intelligence, cloud computing, digital twin technology, 3D printing, edge computing, Internet of Things, and many others — are being applied in many solutions. For example, in the past it would be difficult to manufacture a wind turbine by moulding steel, but with today’s 3D printing technology it becomes much easier, and a much more viable solution for clients. Another example would be the growing adoption of cloud computing. Data logging used to be tedious, and it was painful to retrieve that data for analysis and generate insights, but now it has become very convenient. Amidst the pandemic lockdowns, cloud-enabled factories were able to continue with their operations even though workers could not report to the physical workplace, because the factories could be operated remotely.
There is also increased emphasis on the development of holistic solutions. Engineering in the past used to be very product or system-centred, where you work on a particular product/system and its corresponding set of “function-feature-benefit”. However, the development of solutions today calls for a more in-depth and comprehensive analysis of the problem. For example, when one is tasked to engineer solutions for a factory, one needs to understand the complexity of the entire factory, before being able to come up with a holistic solution that can address the root cause of the issues faced by the client.
How will the job landscape of the manufacturing industry change in the coming years?
Firstly, we would be seeing a growing number of females working in the manufacturing sector. There weren’t as many females in the past, but with the changing nature of the work — not just creating a product through manual labour, but analysing entire businesses and value chains in order to create holistic solutions — there is increasing realisation that the sector does not necessarily need to be male-dominated. It is exciting that manufacturing is becoming less gender-biased, and it is a positive trend that we see more female engineers well-equipped in STEM joining the field.
Secondly, digitisation means that the industry is ripe for disruption by youths. This is an encouraging development for youths, as the barrier to entry of the industry is lowered. Industry stalwarts cannot simply rest on their laurels and instead have to keep up with technological advancements. Manufacturing is increasingly demanding new skills involving technology, which youths may have an advantage in.
Thirdly, generative design technology will allow us to design, build, and operationalise factories in a much shorter timeframe. With current technology, it would only take two years, compared to the five year average in the past. You do not need to sequentially design the factory, build it, slowly bring in the physical equipment, before figuring out how to automate your factory processes. Today, you are able to complete the process on a digital twin beforehand, by testing the factory design in the virtual world, visualising the entire throughput of material, and calculate the factory’s overall productivity — all before even starting construction. By having drawn up the plans and completed the calculations digitally, the factory can maximise its productivity levels right from the start. This is a welcome phenomenon as newcomers to the industry do not necessarily have to be afraid of existing players in the industry. While existing players may have many years of experience under their belt, they may not have kept up with technological advancements which are becoming increasingly important.
What are the skills that are going to become more in-demand?
The skills in demand are changing, with a shift from physical execution towards analysis. Large amounts of data is being collected from sensors and consumer markets, and one needs to be able to analyse that data to derive insights. This will allow you to decide what you are going to manufacture in a week, a month, or a year from now.
Employers are also looking for a positive work attitude in potential hires. These include traits such as being proactive, thinking in advance, showing initiative, and embracing lifelong learning. One needs to be adaptable and comfortable with a constantly changing environment. If you are an executive in manufacturing, you will need to be able to frame the big picture of where your manufacturing company should be going.
What are some challenges you face in your job?
One challenge we face is that many clients often hesitate to invest in digital solutions, despite being interested in digital transformation. This is especially true for firms that have been in operation and successful for over 20 years. The challenge is that the client needs to have that drive at the top to push for digitalisation. This challenge is more pronounced because we operate in a region where countries vary greatly in their levels of technological advancement. While clients in Singapore may be comfortable with high-tech solutions, clients from other countries may be more resistant or unconvinced by our sales pitches as they are less familiar with adopting such technology. Thus, it requires a lot of in-depth effort to understand and analyse the client’s unique circumstances, and assist them in recognising the long-term benefits of digitalisation. While you may have a solution to offer your client, you need to be able to curate and frame it well, in order to persuade your client to adopt it.
Another challenge that we face is attracting good talent, but the situation is improving. With more and more exciting work becoming available in manufacturing, we see this problem being a smaller issue. We need to better publicise the exciting and dynamic transformations happening in the industry, in order to better attract youths to join.
What made you decide to join, and subsequently stay on, in the industry?
The work is exciting and interesting. Every problem a client presents is unique, and creating a holistic solution that fits their needs will always be new and interesting. Most manufacturing MNCs also offer ample opportunities for frequent rotation, allowing you to change your role every few years, which keeps work exciting. The manufacturing ecosystem in Singapore is also big enough for you to move from company to company, which exposes you to the full dynamism of Singapore’s manufacturing landscape. International exposure and the opportunity to work in multiple countries was also a draw.
The work is also deeply meaningful. Manufacturing involves working with real things that you can feel and can touch, be it your everyday gloves, cars, or servers. But it also impacts real lives and improves them. It allows you to be on the frontlines talking to people involved in the day-in-day-out, who intimately know what the pain points are, which you can resolve through the solutions you manufacture. For example, a simple manufacturing solution to improve satellite signal penetration can greatly boost access to information for rural communities. You have the opportunity to travel to these countries to actually implement these solutions, and observe the value add to these people’s lives. Once you see the big picture and the meaningful impacts that manufacturing can create, you begin to appreciate the small details of your work.
How did Covid-19 feature in the work that you do?
Covid-19 really highlighted the importance of manufacturing. When the pandemic struck, a client needed us, as their manufacturer, to ramp up the production of a component product used in critical medical equipment by over eightfold in a short span of time. More parts being produced meant more lives being saved. The small yet crucial role we as manufacturers played in supplying this product made a difference as to whether the medical equipment could be used in hospitals.
There was also the shortage of masks. While we as an electronics manufacturing company could not directly apply our technology to the need, we were able to identify a common link – that masks needed extremely clean environments to be manufactured in, similar to LCD technology. Hence, in other countries (outside of Singapore), we sourced for the necessary equipment and then pivoted our manufacturing sites towards producing masks.
We also see clients shifting mentalities from “just-in-time” to “just-in-case”, and seeking to boost resilience amidst supply shocks like the pandemic.
These small yet impactful moments that often arise in one’s manufacturing career really allows you to realise that what you do actually makes a difference. Rather than simply focusing on the technology or the profit we are generating, it is fundamentally about touching lives.
What advice would you give to youths considering a career in manufacturing?
If you are deciding on a specific area in manufacturing where you could start a career, you could consider starting out in an area with high variance and high digitalisation. This is where you learn the most, and it also becomes easier to later cope with the low variance and low digitalisation work, because the reverse is tougher. For example, high variance and high digitalisation industries include semiconductor manufacturing, while low variance and low digitalisation industries include maritime manufacturing.
As the manufacturing industry is very varied, it is crucial to learn skills that are applicable across different industries. Do not spend too much time focusing on the knowledge specific to only one niche industry (e.g. the fine details of how to manufacture a semiconductor), that you forget to pick up broader skills such as methodologies and systematics applicable to every industry. This will allow you to switch careers and industries more easily.
Learn how to launch a new product, such as how to draft a “four 4 P plan” (product, price, place, promotion), how to plan revenues and expenditures, and how to make benchmarks. Learn what are benefit expectations, as well as commercial and technical success factors. Understanding these systematics and methodologies will allow you to become independent of the industry you are currently in, and flexible in terms of developing your career in the future.
Be wary of superiors placing you in positions where you will likely stagnate, such as those that acquire only very specific micro skills relevant to one industry but irrelevant to others. When the work becomes unexciting, leave. Prioritise your creativity and freedom to try new things, and seek a good management that will allow you to explore.
Overall, remember why you do what you do, which is what differentiates us humans from machines. The specific situations and problem sets changes, but remember why you want to help the world create solutions through manufacturing.