Conversations with Dallan Seah
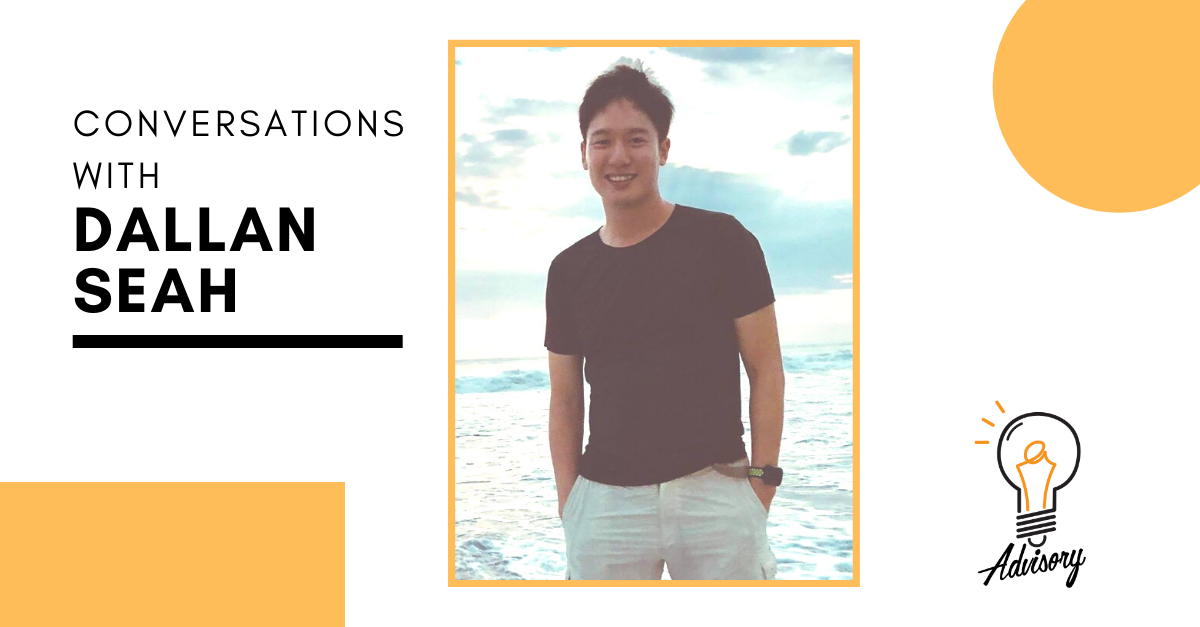
By Darrius Tan
Dallan Seah is a Manager, Manufacturing Sciences & Technology (MS&T) at Moderna, where he was based in Cambridge, Massachusetts at one point and served as the Lead Tech Transfer and in-charge of scaling up the (Covid-19) mRNA-1273 LNP Vaccine for commercial manufacturing. Before that, he worked at Novartis for 4 years where he took on various roles in MS&T, such as manufacturing support, process troubleshooting, investigation, and process monitoring.
Dallan graduated from the National University of Singapore with a Bachelor of Engineering (Honours) in Chemical and Biomolecular Engineering. He has also taken various courses at the Harvard Medical School, including courses on Cancer Genomics, Immunology and Drug Delivery.
As a Manufacturing Sciences & Technology Manager, how would you describe your typical workday?
I am a MS&T manager at Moderna’s Norwood manufacturing facility, which works round the clock, 24 hours a day, 7 days a week. This role involves working with my team to provide round-the-clock manufacturing support, and to ensure that our product meets the highest quality standards.
In our work, we also look into the future, thinking about how to continuously improve the vaccine manufacturing process for yield and robustness. In doing so, we have to collect science-based evidence, perform validation, and consider risk management strategies. This often requires close collaboration with a wide variety of stakeholders; a significant portion of each workday is dedicated to meetings to collaborate and connect with our partners. In addition, I also make it a point to catch up with my manager and direct reports. In a pandemic, one is easily motivated in our line of work and you get burnt out before you know it. I have regular touchpoints with my direct reports to ensure they are level loaded and they have what they need to achieve work-life balance.
Recently, I transitioned into a new role in Moderna, where I am now based in Singapore. In this position, I work with international partners to start up other Contract Manufacturing Organisation (CMO) sites, as we continue to scale-up our vaccine manufacturing operations.
What were some of the most interesting projects that you have worked on before this (e.g. at NUS, at Novartis)?
One of the most interesting projects that I have worked on was a design project in National University of Singapore (NUS). The objective of the project, often the penultimate act in most Chemical Engineering curriculum, is to design a chemical plant in simulation and optimize for a number of factors, such as profit and safety, as a team. This paper exercise put me through the paces of engineering design concepts, methodologies and philosophies, something that I see myself practicing and refine repeatedly in my career. More importantly, this project highlighted the importance of teamwork and a strategy of playing to the strengths of each team member; these are principles that are well-mirrored in real world project teams.
Apart from this, another interesting project that I undertook is performing a Computational Fluid Dynamics (CFD) model for the bioreactors in Novartis. As part of this project, there was a need to retrofit the agitator, alter design and location of the bioreactor and recommend setpoints; as a result, oxygen transfer could be maximised and the yield of product increased significantly.
What are some of the important lessons that you have learnt from your working experiences?
First, while it is important to know as much as you can, it is more important to know what you don’t know, and this requires humility and courage.
Second, while the pharmaceutical industry has lots of norms and standards, assumptions behind norms and standards can change as the industry and technology constantly evolve. As such, critical thinking is needed to challenge assumptions and make considered and informed decisions. Do not reinvent the wheel if you can, but do so if you must.
Is there something you look out for when you bring new people on the team?
First, I expect interviewees to come prepared with a good background of the company and technology and good questions. A future employee who does not prepare for the interview will probably not prepare for future meetings and projects. Doing the research and asking good questions also reflect good curiosity, which is a valuable trait in our line of work. It is also important to be familiar with one’s experiences and past work. For instance, some interviewees may not know the product they worked on as well as they should have. This is a good barometer for assessing involvement and ownership for past projects.
Second, we look at their personal qualities to see if they are suited for the job they apply for. Preferably, interviewees should be curious and have a hunger for learning. The pharmaceutical industry is very dynamic, and technology evolves quickly all the time. As such, the willingness to explore new ideas and to adopt new practices quickly is important. I have been directly and indirectly involved with five (5) to six (6) facilities, with up to twenty (20) processes and have learnt something from each of them.
In addition, interviewees should be relentless. Folks need to be motivated to do what it takes to produce the best possible outcomes for our patients. In short, an ideal interviewee should have a deep, intrinsic motivation to achieve their goals, and have a drive to learn voraciously.
How would you describe the working culture in Massachusetts, where you’re based? Are there any differences with that of our local workplace culture?
Boston, the area I was based for the past few years of my working life, has a vibrant biomedical and pharmaceutical scene, and a lot of startups in this field are based there. Many world class universities attract top talent around the world, such as Harvard, MIT, and Boston University. There is a constant vibe to do things bigger, better, and faster, which acts as a strong motivation to innovate and develop new ideas. People also tend to move around different companies pretty frequently, which allows cross-pollination between companies and extensive exchanges of ideas, therefore enhancing human capital.
On the other hand, Singapore features more Multinational corporations (MNCs) with more established corporate standards and norms. Moreover, these compan#ies view Singapore more as a manufacturing hub than an innovation hub, and the local startup scene is definitely less established. The result is a more risk-averse attitude in the Singapore work culture. This is not necessarily good or bad, just simply two cities featuring different value propositions to different types of companies.
However, this may change in the long-run, as Singapore is trying to build up innovation capabilities in this industry. I look forward to this shift too.
What advice would you give to yourself in retrospect before entering the working world?
One piece of advice I would have given myself is to consider taking a break between graduation and my first job. After graduating from college, I went into the workplace directly. Working life is hectic, and perhaps taking a break before entering the working world would have given me the opportunity to knock out some bucket list items before life gets in the way.
Is there any advice that you would like to share with students who are looking to join this industry?
First of all, chemical and biomolecular engineering is a degree with huge utility professionally and in life! It is definitely a fulfilling and exciting option to consider seriously.
My advice to students is to keep their options open when looking for different careers in Chemical and Biomolecular Engineering, and to pursue various opportunities to gain a deeper appreciation for different career pathways. As a student, I was grateful that I had various opportunities which allowed me to explore the various facets of this subject, such as doing H3 Pharmaceutical science in Junior College and conducting a research stint in Massachusetts Institute of Technology (MIT) as an undergraduate. These opportunities did have a bearing on my decision to carve out a career in pharmaceuticals. In my time, there were many other attractive sectors, such as the chemical, semiconductors, or oil and gas industries, but choosing pharmaceuticals was certainly a choice that worked out for me!
Students can also afford to be bold, to go with what interests them the most after considering their strengths and aptitudes in various fields thoroughly. For instance, when I joined Moderna, I relocated from Singapore out of big pharma to join a lesser-known start-up. In the three years that I have joined, Moderna has witnessed tremendous growth, and it has certainly become a mainstream player in this field. In short, be bold and enjoy the ride.
Last of all, always remember the things you learn in school, because these skills are very transferable to the workplace and life in general.